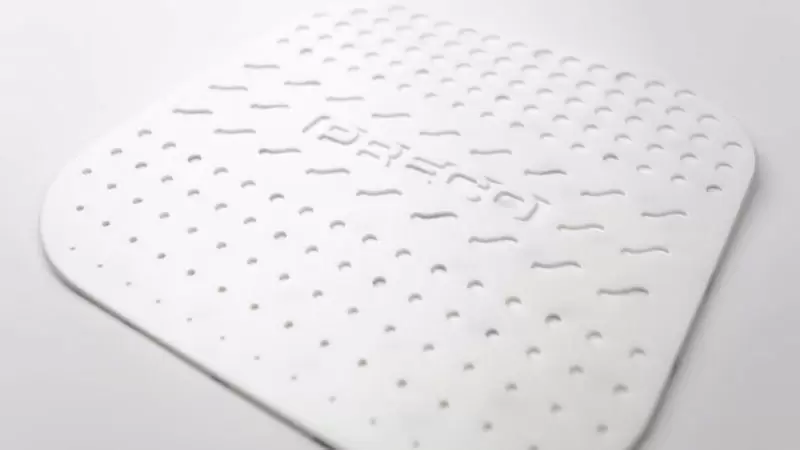
Laser and Die Cutting Foams
The variety of foams on the market including reticulated foams, open-cell foams and closed-cell foams that are routinely die cut however they can also be laser processed. Die cutters need systems that provide a clean and accurate cut part that reduces concavity in the processing. The benefit is more precision—part-to-part accuracy and tighter tolerances of parts cut.
Applications
- Sporting Goods
- Appliances
- Small Engines
- Cosmetics
- Gaskets
No hassle processing.
Converters who die-cut PSAs deliver benefits to their customers, including unique shapes, waste reduction, automated processing, and improved end-product quality. To meet the needs of converters in these markets, Preco incorporates die-cutting techniques and processes such as kiss cutting, matrix removal, rewind, unwind, de-slugging, knock out and stacking, collating. Laser processing PSAs and/or labels offer flexibility, precision and repeatability without the traditional limitations of other methods.
Preco die cutters can kiss-cut to the liner with an ultra-accurate micrometer stop when cutting different types of Foams.
INDUSTRIES
- Aerospace
- Automotive
- Agriculture
- Cosmetics
- Electronics
- Medical
- Packaging
MATERIALS
- Silicone Sponge
- PU Foam
- Open Cell Sponge Rubber
- PVC Foam
- PE Foam
- PS Foam
Laser Processing
Some of the many advantages of Laser Processing foams.
- Non-contact processing
- Reproducible precision down to ±0.051 mm
- No tool wear - laser is always sharp
- Fine details without breakage
- Flame-polished edge in one step
- Eliminate chipped edges
- Speeds up to 25m/second
- Square corners inside or out
Die Cutting
Some of the many advantages of Die Cutting foams.
- Accommodates varying material thickness up to 4" thick on the same system with Preco adjustable roll feeds.
- Systems can be fitted with programmable heated platens to aid in sealing or open and closed cell foams, and other heat-sensitive material
- Increased steel rule die life through accurate control of cutting depth via the powered Micrometer Ram Adjustment.
- Material stretch eliminated, deformed parts avoided by use of Preco presses that have a synchronized feed system.
- Increased system versatility. Preco presses handle both sheet and roll material.
- Simultaneous kiss cutting and through cutting possible with accurate depth control via Micrometer Ram Adjustment.
- Increased yield with closer nesting of parts through the Preco material handling system
- Die can be changed in a matter of seconds without tools through the use of swing-away roll feeds and pneumatic quick-change steel rule die clamps. Preco's microprocessor can store jobs in memory.
- Can handle parts with facings or pressure-sensitive backings.
- Custom-built for all industries and markets with help from Preco's Engineering and Design team.