LASER HEAT TREATING SOLUTIONS
At Preco, we understand the importance of precision and control in material processing. Laser heat treating (also known as laser hardening), makes surface modification easy with targeted transformation and cleaner processes that are efficient, repeatable, adaptable, and deliver superior quality and performance.
The advantage of the laser heat treating process is the ability to harden localized areas without affecting the entire workpiece. Drive your business forward with the most advanced laser hardening solution - Go Preco!
WHY CHOOSE LASER HEAT TREATING?
Our advanced laser hardening solutions offer unparalleled benefits.
Greater Control
Achieve precise heating patterns tailored to your specifications.
Selective Heating
Target hard-to-reach areas with ease, ensuring uniform treatment throughout.
Localized Thermal Impact
Eliminate the need for post-machining with self-quenching heat removal.
Quality and Performance
Attain superior results with our cutting-edge laser technology, including high hardness, increased wear resistance, restored ductility, and improved formability.
Minimal Distortion
Maintain the integrity of your components with minimal to no warping or distortion.
Pinpoint Accuracy
Deliver energy directly to the microstructure to treat material properties without affecting surrounding areas.
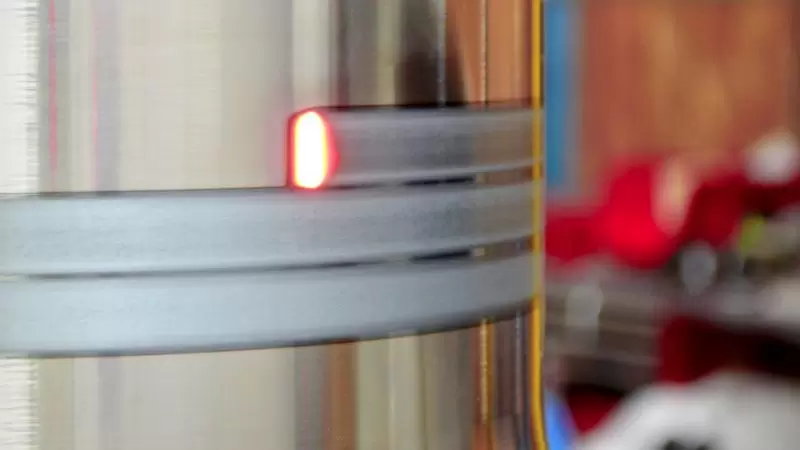
For All Your Material Processing Needs - Go Preco!
Experience unmatched precision, control, and quality along with the reliability, expertise and cutting-edge innovation you expect from Preco.
Laser Heat Treating VS. Induction Heat Treating
While both laser hardening and induction heat treating offer advantages in material processing, understanding their differences can help you make the right choice for your application and drive value for your business.
LASER HEAT TREATING | INDUCTION HEAT TREATING | |||
Energy Source | Laser technology provides focused energy delivery | Electromagnetic coils induce heating in materials | ||
Control and Precision | Precise targeting of specific areas for transformation; unmatched control over heating patterns | Uniform heating of larger surface areas; limited control over heating zones | ||
Accessibility | Able to reach and treat hard-to-access areas with ease | Limited in treating complex geometries or tight spaces | ||
Speed | Rapid heating and self-quenching for efficient processing | Heating and cooling times vary depending on part size and complexity | ||
Distortion | Minimal to no distortion due to localized heating | Potential for distortion especially in larger parts | ||
Sustainability | Energy-efficient, minimal waste generation, and low environmental footprint | Increased energy wastage and waste generation due to the need for uniform heating across larger surfaces | ||
Automation | Easily automated, enhancing efficiency and reducing labor costs | Can be limited depending on the degree of automation built into the equipment | ||
Maintenance | Generally lower setup and maintenance requirements | Requires periodic maintenance of induction coils |